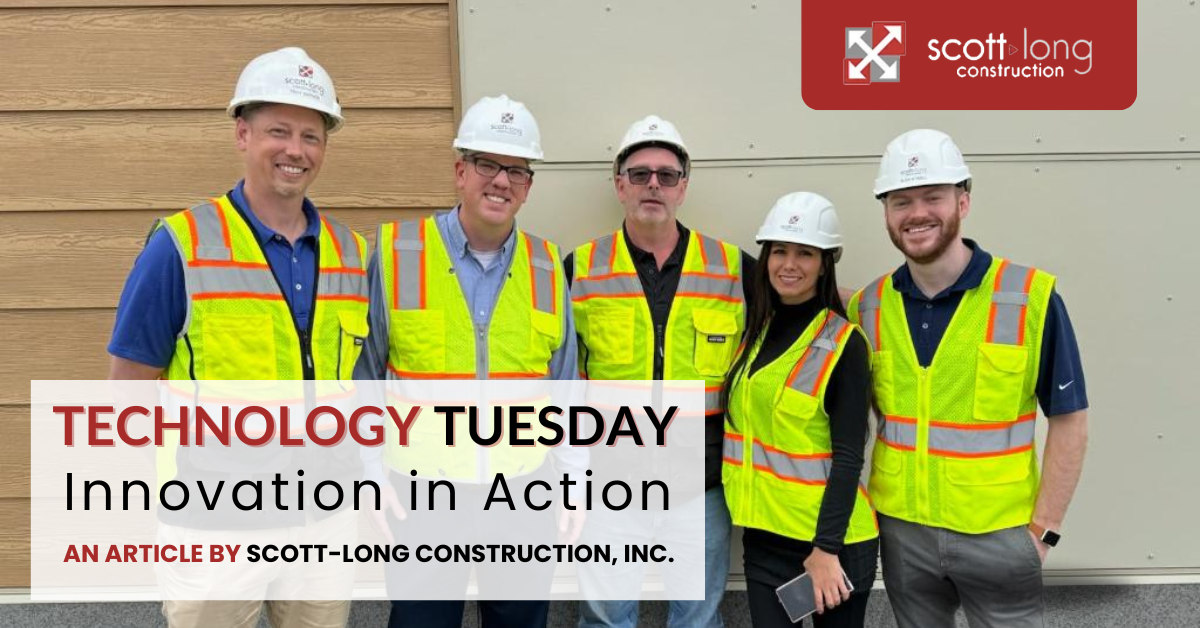
Fiber cement siding products by James Hardie are deservedly legendary for their beauty and high performance. But like any project, installing them to manufacturer specs and delivering a beautiful exterior can take planning and collaboration.
For the Evergreen Village retail project in Manassas, Virginia, developed by Aksoylu Properties LLC, Scott-Long Construction was tasked with installing Hardie Architectural Panel siding. During the process, the Scott-Long team identified a challenge: the fastener pattern needed precise management to meet the manufacturer’s installation specifications while ensuring the design’s intended aesthetic and long-term value. Every job presents its own set of challenges, and it’s up to the professionals to find the right solutions when issues arise.
Mosely Architects, Scott-Long Construction and Jose Construction had a strong rapport for problem-solving: Vendors stayed in close contact during the submittal, material release and delivery, installation, and quality control steps, with daily photos tracking the progress of installed materials.
Collaborating and Solving
For the fasteners to align properly, teams had to align, as well: Upon spotting the issue with fastener alignment, Scott-Long consulted with onsite teams and James Hardie product specialists. It was important to define an efficient and thorough QC process that would deliver quality—and not hold up other vendors or jeopardize the project timeline.
- The butt joints of the lap siding elements would have to be straight-cut for proper alignment while also taking into account the effects of weather exposure.
- Hardie Architectural Panel siding: While trim covers all edges, the fastening system was a reveal-exposed mechanical fastener application. Aligning building features with manufacturer requirements meant multiple methods for sinking screws had to be evaluated.
- String line was used vertically and horizontally to incorporate a true straight line for a fastening pattern, installation, and trim straight line.
- Upon QC review, a separate crew chased the initial installation to place remaining fasteners and make corrections as needed. This way, the trim reveal system was able to match the agreement all parties’ made during initial review.
Adjustment Easier to Make With Proper Front-End Process
Adaptability is easier to pull off with correct preparation beforehand. Prior to surfacing the screw alignment concern, Scott-Long worked with stakeholders and other trades to review manufacturer materials, provide layouts, and back blocking. Quadrant-by-quadrant mockups were generated so that satisfactory completion of the first quadrant would set a standard and process for remaining quadrants. Among other things, this allowed Jose Construction to get the initial siding elements in place as quickly as possible.
Every team on a project—and, ultimately, the developer or project owner—benefits from a deeper shared understanding of the complex overlays of installation, planned architectural features, quality control, and manufacturer’s requirements. The best-laid plans include a detailed view of conditions specific to the project, trim features, and how they will impact the schedule and execution of all the trades who must collaborate to execute the vision correctly.
Ready to take your next project to the next level?
Partner with a team that understands the importance of precision, collaboration, and quality control. Contact Scott-Long Construction today to discuss how we can help bring your vision to life, ensuring every detail is executed flawlessly. Let’s build something exceptional together.